HISTORY OF FINNFOAM OY
HISTORY OF OUR DEVELOPMENT
The production technology used in the manufacture of FINNFOAM utilizes carbon dioxide generated as an industrial byproduct as the propellant. Carbon dioxide has been recycled at Finnfoam for more than 20 years. The production of FINNFOAM XPS insulation products has been completely free of HFCs since 2002. In fact, Finnfoam was the first XPS insulation manufacturer in the world to fully eliminate HCFC compounds from the production process.
Finnfoam Celebrated Its 40th Anniversary in 2022
A three-year research and development project for chemical recycling was completed and the construction of a chemical recycling plant began in Salo.
Finnfoam acquired one half of PS-Processing Oy, which specializes in the recycling of polystyrene insulation materials.
New product: FF-FRAME auxiliary frames produced using surplus material from production was introduced to the market at the beginning of the year.
In 2021, Finnfoam grew its operations in Sweden by acquiring 100% of the shares of Cellterm AB. With this, Finnfoam Group reinforced its competitive ability and boosted its growth as a manufacturer of mold-proof plastic insulation materials in the market region surrounding the Baltic Sea.
New product: Roof insulation FF-EPS 60S SILENT was introduced to the market and utilized in the first projects. The new product has attracted significant interest, and it was developed as a response to various challenges and requirements in the industry.
In 2020, Finnfoam introduced the new FF-FLOOR construction solution, which uses 30% less concrete than traditional methods.
In the spring of 2019, Finnfoam became the first Finnish operator to launch a recycling system for plastic insulation waste. FF-Kierrätyssäkki recycling bags are used to collect plastic insulation waste at both construction sites and hardware stores, and the collected waste is reused as material in our plant in Salo.
Finnfoam acquired 100% of the shares of Estplast Tootmine Oü in Estonia.
In 2018, Finnfoam Oy acquired 100% of the shares of Styroplast. With the acquisition, Finnfoam Oy’s range grew to include white EPS insulation, which is a mass product used on construction sites.
Finnfoam’s new training facility FF-AKATEMIA was also completed at the company’s plant in Salo.
In 2017, Finnfoam Oy cooperated with StealthCase Oy to develop the FF-SIGNAL amplifier. FF-SIGNAL is a passive signal amplifier that can be used to enable high-performance internal networking in challenging projects as well. FF-SIGNAL was awarded the Teknologiasta Tuotteiksi Foundation award for the promotion of sustainable and productive built environment in 2017.
In 2017, the FF-XPS 200 LATTIA insulation panel was created as the result of extensive product development. FF-XPS 200 LATTIA is a cost-effective product that is perfect for thermal insulation of slab-on-ground foundations subject to light loads.
The plant in Kristinehamn, Sweden, became operational. Finnfoam Oy also continued to invest in the environment with the construction of a new solar power plant with a surface area of more than 2 000 m2 (351 kWp) next to the company’s production facility.
In 2016, Finnfoam responded to the increasing demand for FF-PIR insulation products by constructing a new heated warehouse for stock products, which also functioned as the first pilot project for the new FF-WALL system.
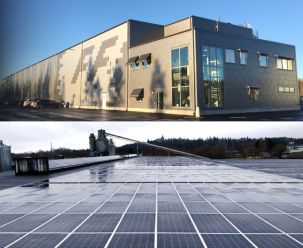
In 2015, construction began on Finnfoam Oy’s new plant in Kristinehamn, Sweden. The Tulppa wet room panel product range was expanded with pre-sloped and floor drain Tulppa panels, which can be used to significantly speed up the construction process and ensures uniform sloping in wet rooms.
In 2014, Finnfoam Oy expanded it product range by introducing the FF-PIR insulation products made from polyurethane. FF-PIR offers effective thermal insulation and safe moisture performance, and it can also be used to ensure that structural thickness remains practical in regular wall or ceiling insulation and various supplementary thermal insulation projects. FF-PIR is also safe in terms of its fire performance, and the fire class of the insulating component of FF-PIR products, i.e., foam, is D-s1, d0, which is among the best in the industry.
In 2013, Finnfoam introduced gray FF-EPS, a new type of product designed for insulating floors, walls, and ceilings.
In 2012, the company was divided into three separate business units. The manufacture of thermal insulation and other construction materials continued as a dedicated enterprise, while the real estate and investment activities were separated into their own businesses.
A new Finnfoam plant became operational in Spain, while Finnfoam Oy started work on new production lines and facilities as part of the most substantial investment of its history. Finnfoam Oy also launched the new Tulppa wet room panels onto the market.
In 2011, Finnfoam’s new plant in Lithuania became operational with a production capacity of almost 500 000 m3 per year in the first stage.
FINNFOAM came first in a frost insulation test conducted by the TM Rakennusmaailma magazine in issue 8/2011.
In 2010, the objectives of the development work that began in 2000 were achieved after various stages. The new lighter variety of F-200 was launched and field testing for new mold-proof insulation products for passive houses commenced. The product is known as F-29, and its thermal conductivity can be as low as 0.029 W/mK in extremely cold conditions.
Lighting in production areas was updated with new, more energy efficient LED lights.
That same year, the Nieminen family started on its first large-scale investment internationally, as construction began on a new plant in Kaunas, Lithuania.
In 2004, FINNFOAM thermal insulation became a CE certified product.
In 2003, the company’s aim was to utilize all characteristics of FINNFOAM effectively in different structures such that the overall cost of the structure could be reduced. Tampere University of Technology was closely involved in the development. One of the new interesting applications identified was the recovery of heat from wastewater.
In 2002, the entire production of FINNFOAM thermal insulation panels moved to new facilities.
The total surface area of the new plant rose to more than 15 000 m2, and the warehouse has enough room for 30 000 m3 of FINNFOAM. The capacity of the new plant increased to more than 500 000 m3. Particular attention was paid to energy efficiency in the design of the new plant. With the new cooling system developed in-house, waste heat can be recovered effectively from the production machinery and transferred to where heat is needed.
Construction began on a new plant in in 2001.
In 2000, Finnfoam was granted a new type-approval for insulation used against the ground with a thermal conductivity of 0.033 W/(mK). That same year, the company launched a development project intended to improve the insulation capacity of air-filled FINNFOAM thermal insulation further by more than 10%, while also lowering the density of the product by more than 20%.
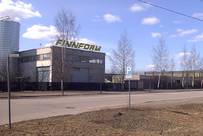
In 1999, polyurethane production was merged with another company in the field. The new enterprise Purtec Oy became one of the largest in its industry in Finland.
In 1998, a breakthrough was achieved in a challenging development project that was launched in 1991. Finnfoam Oy succeeded in producing the first FINNFOAM thermal insulation panels using carbon dioxide. Over the next year, all production lines were converted to use the new propellant that does not impact the environment further. In fact, Finnfoam Oy was the first manufacturer in the world to completely eliminate HCFC compounds from production.
In 1991, the company obtained a new production line with a capacity that matched the total capacity of the lines used previously. That same year, development work began to find an environmentally friendly replacement for the HCFC propellant.
In 1990, Finnfoam Oy began to manufacture pipe insulation and joint filler products from polyethylene using an extrusion-based method as well.
In 1989, Finnfoam Oy became the first manufacturer in the world to replace the CFC compounds used in the production of XPS panels with HCFC compounds. The environmental impact of a HCFC propellant is approximately 5% of the impact of CFC compounds. As HCFCs were quite rare at the time, their availability was very limited and it was still necessary to use some CFCs in production.
In 1988, Finnfoam Oy also began to manufacture various products from polyurethane, such as seating for buses.
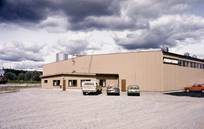
In 1986, the company purchased a new production line with a capacity that was twice the capacity of the existing one, which also remained in used. In-house development made it possible to manufacture parts of the machinery in Finland. The number of employees increased to more than ten. Work on expanding the production plant also began that same year.
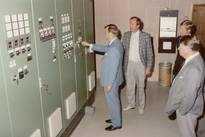
In 1982, Finnfoam Oy was established and began manufacturing extruded polystyrene (XPS). That same year, Stynix Ky was sold to Yhtyneet Paperitehtaat Oy, and the owner Jorma Nieminen turned his focus solely on FINNFOAM production.
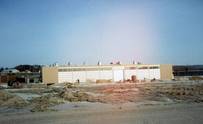
In 1982, Jorma Nieminen became familiar with a new manufacturing method that could be used to produce uniform and closed cell structures. He saw immediately that this product was much better suited for frost proofing than expanded polystyrene (EPS). The new product also offered significantly better strength characteristics than expanded polystyrene, and would thus be much better suited for frost proofing on railway lines. One negative aspect of the new product was the price of the production machinery, which exceeded the price of the equipment used for manufacturing expanded polystyrene by more than tenfold. Nevertheless, Nieminen decided to purchase equipment with a production capacity of more than ten times the market at the time.
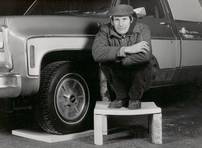
Expanded polystyrene was manufactured using pentane as propellant, which is a highly flammable gas. In 1980, the plant was devastated by a quickly-spreading fire that originated from a hot wire foam cutter. The fire destroyed the plant completely, and badly damaged the expansion being built at the time. Clearing-up operations and the construction of a new plant began as soon as the smoke had cleared. The new plant was commissioned six months after the fire.
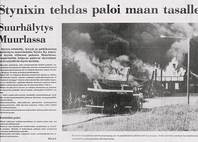
In 1975, Jorma Nieminen founded Stynix Ky, which began manufacturing expanded polystyrene in Muurla, in a facility that had previously housed a dairy. Expanded polystyrene was used to produce, among other things, thermal insulation boards, packaging, pipe trenches, and containers designed for keeping cooking pots warm, which were named “Muhis”.
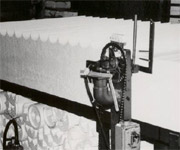
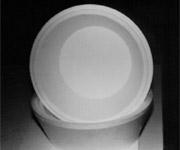
In 1971, Jorma Nieminen began manufacturing pipe trenches from expanded polystyrene (EPS) using equipment he himself had built.